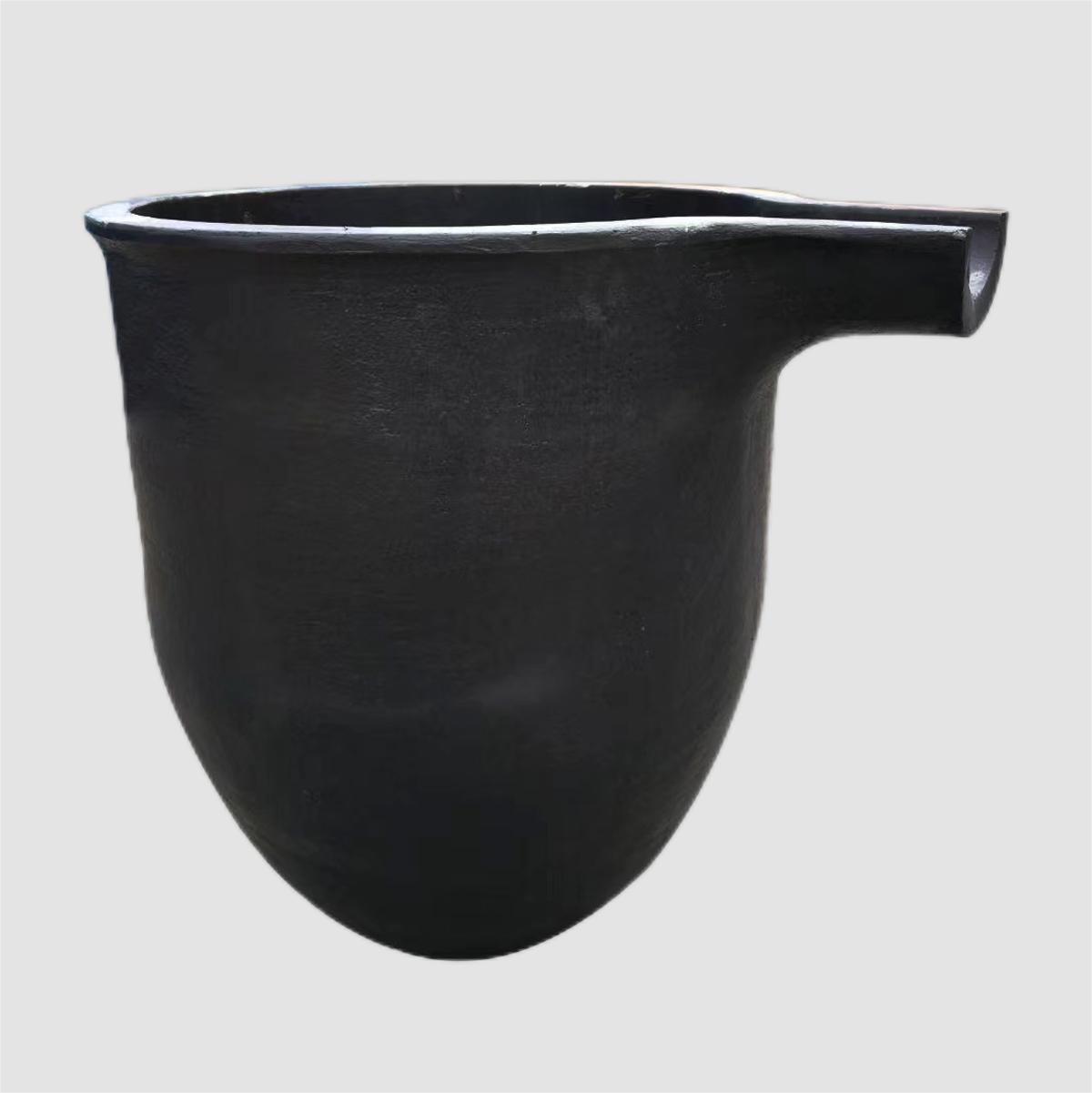
1.4 Sekundarno brušenje
Pasta je zdrobljena, zmlela in presežemo v delce več na stotine mikrometrov, preden jo enakomerno mešamo. Uporablja se kot stiskalni material, imenovan stiskalni prah. Oprema za sekundarno brušenje običajno uporablja navpični valjčni mlin ali žogico.
1.5 Oblikovanje
Za razliko od navadnega ekstruzije in oblikovanja,Izostatični stiskalni grafitnastane s pomočjo hladnega izostatskega stiskalnega tehnologije (slika 2). Surovino napolnite prah v gumijast kalup in prah stisnite skozi visokofrekvenčno elektromagnetno vibracijo. Po tesnjenju sesate delce prahu, da izčrpate zrak med njimi. Postavite ga v visokotlačno posodo, ki vsebuje tekoče medije, kot sta voda ali olje, pritisnite na 100-200MPA in jo pritisnite v valjast ali pravokotni izdelek.
Po Pascalovem načelu se pritisk uporablja za gumijast kalup skozi tekoči medij, kot je voda, tlak pa je v vseh smereh enak. Na ta način praškasti delci niso usmerjeni v smeri polnjenja v kalupu, ampak so stisnjeni v nepravilni razporeditvi. Čeprav je grafit anizotropni v kristalografskih lastnostih, je na splošno izostatični tiskalni grafit izotropni. Oblikovani izdelki nimajo samo valjaste in pravokotne oblike, ampak tudi valjaste in lončene oblike.
Izostatični stroški za oblikovanje se uporablja predvsem v prašni metalurgijski industriji. Zaradi povpraševanja po višjega cenovnega razreda, kot so vesoljska vesolje, jedrska industrija, trde zlitine in visokonapetostne elektromagnetne, je razvoj izostatične tehnologije za stiskanje zelo hiter in ima možnost izdelave hladnega izostatskega stiskalnega stroja z delovnim cilindrom notranjega premera 3000 mm, višine 5000mm in višine 5000mm, višine 5000mm in višine 5000mm in višine 5000mm in višine 5000mm in višine 5000mm in višine 5000mm, višine 5000mm in višine 5000mm in višine 5000mm in višine 5000mm in višine 5000mm, višine 5000mm in višine 5000mm, višine 5000mm, in višino 5000mm in 5000mm. Trenutno so največje specifikacije hladnih izostatskih stiskalnih strojev, ki se uporabljajo v industriji ogljika za proizvodnjo izostatskega stiskalnega grafita, φ 2150mm × 4700 mm, z največjim delovnim tlakom 180MPA.
1.6 Peka
Med postopkom praženja se med agregatom in vezivom pojavi zapletena kemična reakcija, zaradi česar se veziva razgradi in sprosti veliko količino hlapne snovi, hkrati pa je bila tudi reakcija kondenzacije. V fazi predgrevanja z nizko temperaturo se surovi produkt širi zaradi segrevanja, v naslednjem postopku ogrevanja pa se volumen skrči zaradi kondenzacijske reakcije.
Večja kot je prostornina surovega izdelka, težje je sprostiti hlapne snovi, površina in notranjost surovega izdelka pa sta nagnjena k temperaturnim razlikam, neenakomerni termični širitvi in krčenju, kar lahko privede do razpok v surovem izdelku.
Zaradi svoje fine strukture je za izostatski stiskalni grafit potreben posebno počasen postopek praženja, temperatura znotraj peči pa mora biti zelo enakomerna, zlasti v temperaturni fazi, kjer se asfaltni hlapni snovi hitro odpravljajo. Postopek ogrevanja je treba izvesti previdno, hitrost ogrevanja ne presega 1 ℃/h in temperaturna razlika znotraj peči manj kot 20 ℃. Ta postopek traja približno 1-2 mesece.
1.7 impregnacija
Med praženjem se nestanovitna snov premogovega katrana odvaja. Fine pore so v izdelku ostale med odvajanjem plina in krčenja volumna, skoraj vse so odprte pore.
Za izboljšanje gostote volumna, mehanske trdnosti, prevodnosti, toplotne prevodnosti in kemične odpornosti izdelka lahko uporabimo metodo impregnacije tlaka, ki vključuje impregniranje naklona premogovega katrana v notranjost izdelka z odprtimi pore.
Izdelek je treba najprej predhodno predgreti, nato pa garati in razmakniti v rezervoar za impregnacijo. Nato se v rezervoar za impregnacijo dodajo stopljeni asfalt s katranom za premogov katran, da se asfalt impregnirajočega sredstva vstopi v notranjost izdelka. Običajno je isostatični stiskalni grafit podvržen več ciklih praženja impregnacije.
1.8 Grafitizacija
Kalcinirani izdelek segrejte na približno 3000 ℃, urejeno razporedite rešetko ogljikovih atomov in dokončajte transformacijo iz ogljika v grafit, ki se imenuje grafitizacija.
Metode grafitizacije vključujejo metodo Acheson, metodo povezave z notranjo toplotno serijo, visokofrekvenčno indukcijsko metodo itd. Običajni postopek Achesona traja približno 1-1,5 meseca, da se izdelki naložijo in odvajajo iz peči. Vsaka peč lahko prenese več ton do desetine ton praženih izdelkov.
Čas objave: september-29-2023